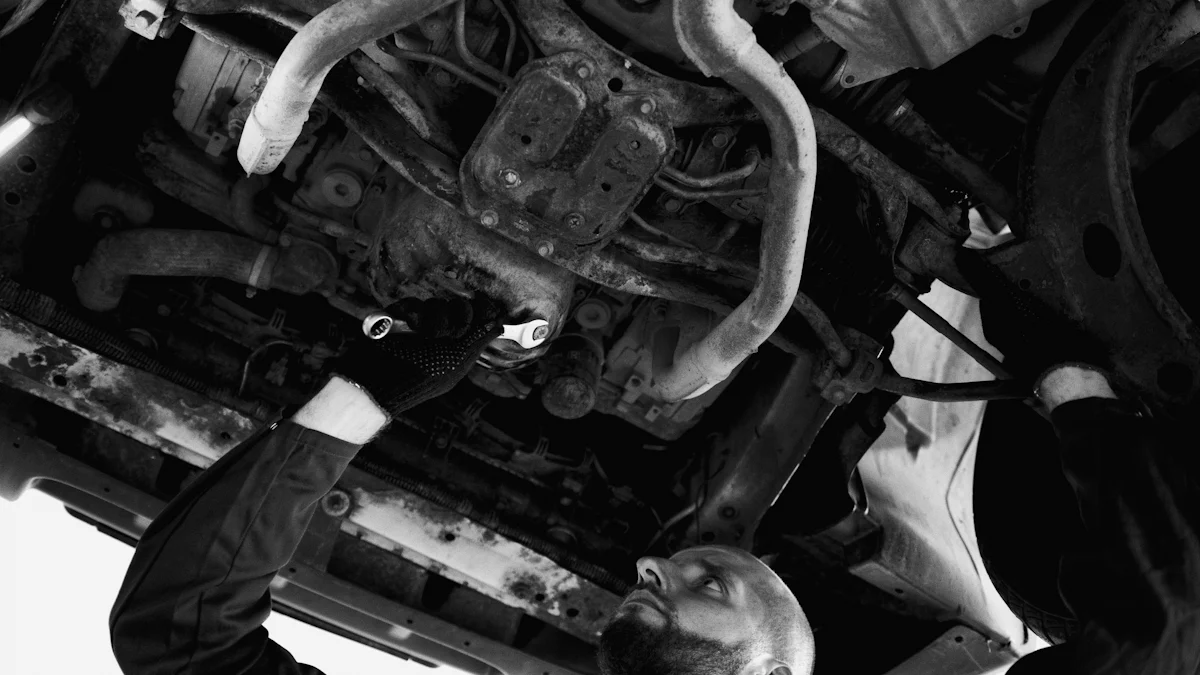
Mini excavator undercarriage parts play a vital role in keeping your equipment efficient and cost-effective. Around 50% of maintenance expenses for track machines come from undercarriage upkeep, making it a significant factor in construction project costs. Proactive care helps you avoid common issues like rust from mud residue or cracks caused by rough terrain. Water exposure and overloading also damage these components, leading to downtime. Regular maintenance ensures your machine stays reliable, reducing repair costs and extending its lifespan.
Key Takeaways
Check mini excavator undercarriage parts often to avoid big repairs. Look at them daily and inspect closely every week or month.
Clean the undercarriage after using it each time. This stops dirt from building up, which can harm parts and cause faster wear. It also helps the machine work better.
Keep the track tight for good performance. Check and fix track sag often to stop extra wear and problems.
Change worn-out undercarriage parts on time. Watch how fast parts wear out and replace them when fully worn to avoid big damage and long delays.
Use strong replacement parts from trusted brands like YNF Machinery. Pick OEM parts for better fit and performance with your machine.
Regular Inspections for Mini Excavator Undercarriage Parts
Regular inspections are essential for maintaining the performance and longevity of mini excavator undercarriage parts. By identifying potential issues early, you can prevent costly repairs, reduce downtime, and ensure a safer work environment.
Key Components to Inspect
Tracks and Track Tension
Tracks endure the most wear during operations. Check for cracks, cuts, or missing links. Improper track tension can lead to premature wear or derailment. Ensure the tension matches the manufacturer’s recommendations to avoid over-tightening or loosening.
Rollers, Idlers, and Sprockets
Rollers and idlers support the tracks, while sprockets drive them. Inspect these components for uneven wear, cracks, or missing teeth. Damaged rollers or sprockets can cause misalignment, reducing efficiency and increasing the risk of breakdowns.
Inspection Frequency
Daily Visual Checks
Perform a quick visual inspection before each shift. Look for visible damage, mud buildup, or loose components. This habit helps you catch minor issues before they escalate.
Weekly and Monthly Detailed Inspections
Conduct thorough inspections weekly or monthly, depending on usage. Check for signs of corrosion, worn-out parts, or misaligned tracks. For heavily used machines, inspect every 1,000 to 2,000 hours to ensure optimal performance.
Tools for Effective Inspections
Using Inspection Tools from YNF Machinery
Advanced tools simplify inspections and improve accuracy. YNF Machinery offers specialized tools designed for mini excavator undercarriage parts. These tools help you identify wear patterns, measure track tension, and establish maintenance benchmarks. Accurate data collection ensures timely interventions, extending the life of your equipment and reducing costs.
Tip: Routine inspections can lower repair bills by up to 25% and prevent delays caused by unexpected failures.
Cleaning Techniques for Mini Excavator Undercarriage Parts
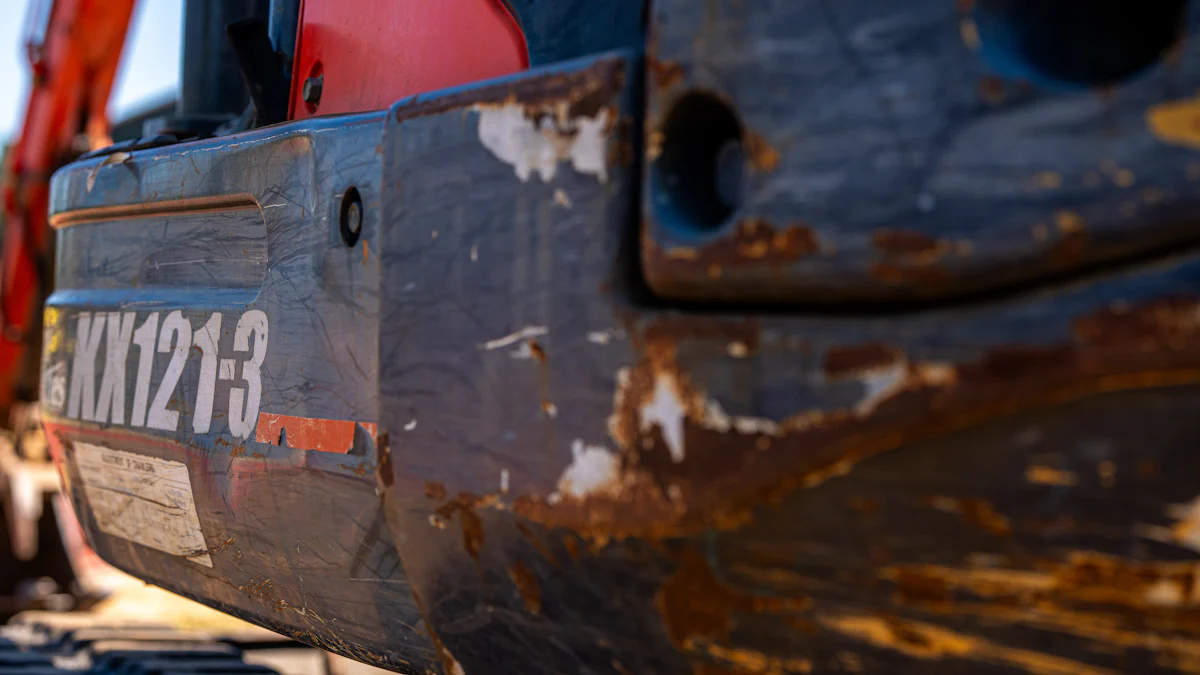
Importance of Cleaning
Preventing Dirt and Debris Build-Up
Keeping the undercarriage clean prevents dirt and debris from accumulating, which can cause significant damage over time. Mud and rocks trapped in the tracks or rollers can freeze in colder climates, damaging bolts and rollers. This buildup also adds unnecessary weight, reducing maneuverability and increasing fuel consumption. Regular cleaning ensures your machine operates efficiently and avoids costly repairs.
Reducing Wear and Tear
Dirt and debris act like sandpaper, grinding against components and accelerating wear. Cleaning removes abrasive materials, reducing friction and extending the lifespan of parts like tracks, rollers, and sprockets. Neglecting this step can lead to uneven wear patterns, misalignment, and eventual breakdowns.
Best Cleaning Practices
Using High-Pressure Washers
A high-pressure washer is one of the most effective tools for cleaning mini excavator undercarriage parts. It quickly removes mud, grease, and debris, even from hard-to-reach areas. Start by lightly hosing down the undercarriage to loosen dirt, then use the pressure washer to target stubborn grime.
Cleaning Hard-to-Reach Areas
For areas that the pressure washer can’t reach, use tools like stiff brushes or undercarriage cleaners. These tools help dislodge debris from tight spaces, ensuring a thorough clean. Applying touchless detergents can also break down grease and minerals, making it easier to rinse away residue.
Tip: Clean the undercarriage after every use, especially if you’ve worked in muddy or icy conditions. This habit prevents long-term damage and keeps your equipment in top shape.
Post-Cleaning Maintenance
Inspecting for Hidden Damage
After cleaning, inspect the undercarriage for hidden damage. Look for cracks, loose bolts, or worn-out components that may have been concealed by dirt. Addressing these issues early prevents them from escalating into more significant problems.
Ensuring Proper Drying
Dry the undercarriage thoroughly to prevent rust and corrosion. Use air compressors or clean rags to remove moisture from metal surfaces. Reapply lubricants to moving parts like hinges and pins to maintain smooth operation and reduce friction.
Note: Regular cleaning and post-cleaning maintenance can significantly extend the life of your mini excavator undercarriage parts, saving you time and money in the long run.
Adjusting Track Tension for Optimal Performance
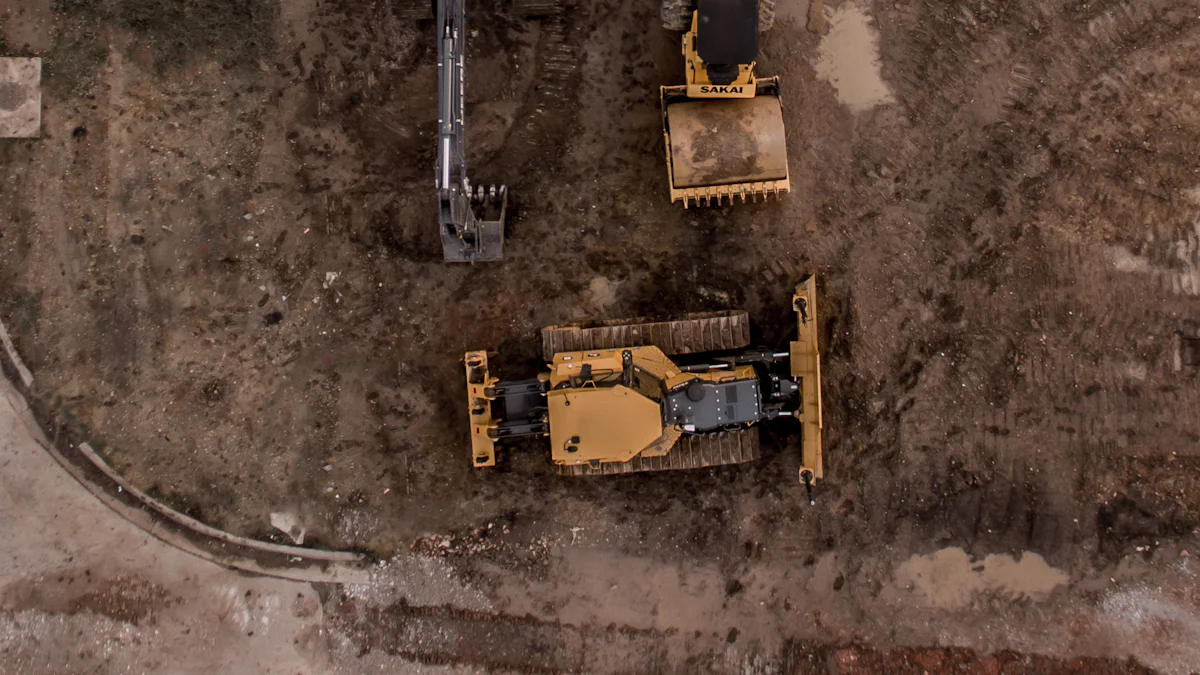
Proper track tension is critical for maintaining the efficiency and longevity of your mini excavator undercarriage parts. Incorrect tension can lead to unnecessary wear, operational inefficiencies, and costly repairs. Understanding the importance of track tension and how to adjust it ensures your equipment performs at its best.
Why Proper Track Tension Matters
Avoiding Over-Tightening
Over-tightened tracks place excessive strain on components like idlers, rollers, and sprockets. This strain accelerates wear and can lead to premature failure. Tight tracks also increase resistance, reducing fuel efficiency and making the machine harder to maneuver.
Preventing Loose Tracks
Loose tracks often slip off rollers, especially on uneven terrain. This slippage can cause downtime and damage to the undercarriage. Loose tracks also wear out pins and bushings faster, leading to higher maintenance costs.
Tip: Signs of incorrect track tension include unusual noise, poor traction, and uneven wear patterns.
Step-by-Step Adjustment Guide
Tools and Equipment Needed
You’ll need a wrench, a measuring tape, and a grease gun. These tools help you adjust the tension accurately and efficiently.
Measuring Track Sag
Press down on the middle of the track.
Measure the sag, which should be between 1-3 centimeters.
If the sag is outside this range, proceed with adjustments.
Adjusting the Tension Bolt
Locate the track tension adjustment cover plate and remove the bolts.
Loosen the locknut on the tension adjustment rod.
Turn the rod clockwise to tighten or counterclockwise to loosen.
Recheck the sag to ensure it’s within the recommended range.
Tighten the locknut and replace the cover plate.
Note: Regularly checking and adjusting track tension prevents operational inefficiencies and extends the life of your tracks.
YNF Machinery’s Role in Track Maintenance
Using YNF Machinery’s Hydraulic Cylinder Seal Kits for Adjustments
YNF Machinery offers high-quality hydraulic cylinder seal kits that simplify track tension adjustments. These kits prevent oil leaks and ensure smooth operation during maintenance. Their durability and precision make them an essential tool for maintaining optimal track tension. By using YNF Machinery’s products, you can reduce downtime and improve the overall performance of your mini excavator undercarriage parts.
Recognizing and Addressing Wear and Tear
Identifying Common Signs of Wear
Cracks or Breaks in Tracks
Cracks or breaks in the tracks often signal the need for immediate attention. These issues usually result from prolonged exposure to rough terrain or overloading. Regularly inspect the tracks for visible damage, as even small cracks can worsen quickly under heavy use.
Worn-Out Rollers or Sprockets
Rollers and sprockets play a crucial role in supporting and driving the tracks. Signs of wear include missing teeth, uneven surfaces, or excessive noise during operation. Strange vibrations may also indicate a worn idler or sprocket, which can lead to misalignment and reduced efficiency.
Uneven Wear Patterns
Uneven wear patterns often stem from improper operation or environmental factors. Common causes include water exposure, rough terrain, and mud residue. These factors accelerate wear on specific areas, leading to imbalances that affect the machine’s performance. Regular cleaning and proper operation can help prevent this issue.
Tip: Look for rust or corrosion on the idler surface, as this can weaken its integrity and lead to premature failure.
When to Replace Undercarriage Parts
Guidelines for Replacement Timing
Industry standards recommend replacing undercarriage parts when they reach 100% wear. Regular inspections help you monitor wear rates and predict the remaining lifespan of components. This proactive approach allows you to schedule maintenance efficiently, minimizing downtime and maximizing productivity.
Evidence Point | Description |
---|---|
Inspection and Monitoring | Regular checks ensure timely identification of worn parts. |
Predicting Residual Life | Monitoring wear helps plan replacements without disrupting operations. |
Cost Reduction | Early intervention reduces repair costs and extends component lifespan. |
Wear Rate Management | Balanced wear across all parts prevents premature failure. |
Risks of Delaying Replacement
Delaying replacement can lead to severe consequences. Worn sprockets and tracks often cause excessive wear on bogies and rollers, resulting in extended downtime. For example, a job initially scheduled for five days could stretch to three weeks due to unforeseen damage. Additionally, ordering replacement parts at the last minute increases costs and disrupts project timelines.
Note: Timely replacement not only saves money but also ensures your equipment remains reliable during critical operations.
YNF Machinery’s Replacement Solutions
Excavator Couplings and Engine Parts for Enhanced Durability
YNF Machinery offers high-quality replacement solutions designed to enhance the durability of your mini excavator undercarriage parts. Their excavator couplings ensure efficient power transmission, reducing the risk of machinery failure. Engine parts like pistons and crankshafts are built to withstand harsh conditions, providing long-lasting performance. By choosing YNF Machinery, you gain access to reliable components that minimize downtime and improve operational efficiency.
Callout: YNF Machinery’s products undergo rigorous quality checks, ensuring they meet or exceed industry standards.
Selecting and Replacing Mini Excavator Undercarriage Parts
Choosing the Right Replacement Parts
Material and Durability Considerations
When selecting replacement parts, prioritize materials that can withstand harsh working conditions. High-quality components, such as track chains, sprockets, idlers, and rollers, should resist wear and tear. Inspect track chains for loose bolts, cracks, or bends. Check sprockets for rounded teeth, which indicate excessive wear. Examine idlers for cracks or oil leaks, and inspect rollers for similar signs of damage. Durable materials ensure long-term performance and reduce the risk of premature failure.
Compatibility with Your Excavator Model
Always choose parts designed specifically for your excavator model. Using genuine parts ensures compatibility and reliability. These components meet or exceed OEM standards, enhancing efficiency and reducing the likelihood of operational issues. Properly matched parts also simplify installation and minimize downtime.
Sourcing Quality Parts
Benefits of Choosing YNF Machinery
YNF Machinery offers a wide range of high-quality replacement parts for mini excavators. Their products undergo rigorous quality checks to ensure durability and performance. With competitive pricing and excellent customer support, YNF Machinery simplifies the sourcing process. Their parts are designed to meet the demands of heavy-duty applications, making them a trusted choice for contractors and equipment owners.
OEM vs. Aftermarket Options
OEM parts provide a perfect fit for your equipment, ensuring optimal performance and reliability. They undergo strict testing and often come with warranties, reducing long-term maintenance costs. Aftermarket options may offer lower prices but can lack the precision and durability of OEM parts. Investing in OEM parts minimizes the risk of performance issues and excessive wear, saving you money over time.
Safe Replacement Practices
Preparing Tools and Work Environment
Before starting, gather the necessary tools, such as wrenches, grease guns, and measuring tapes. Wear protective gear, including gloves, goggles, and steel-toed boots. Ensure the machine is powered off and stable. Use wheel chocks or blocks to secure it in place, and release all hydraulic pressure from the system.
Step-by-Step Replacement Process
Inspect the damaged part, such as a track chain or sprocket, for wear or cracks.
Remove the worn component using the appropriate tools.
Clean the area to remove debris or grease. Avoid harsh chemicals that could damage surrounding parts.
Install the new part, ensuring proper alignment and secure fastening.
Test the machine to confirm smooth operation.
Post-Replacement Maintenance Tips
After replacing a part, inspect the surrounding components for hidden damage. Lubricate moving parts to reduce friction and ensure smooth operation. Regularly monitor the new part for signs of wear to catch potential issues early.
Tip: Avoid common mistakes like using improper tools or skipping safety precautions. These errors can lead to injuries or damage to your equipment.
Regular maintenance of mini excavator undercarriage parts offers numerous benefits. It extends the lifespan of components, reduces downtime, and lowers operating costs. As one expert insight notes:
Proper maintenance will help extend undercarriage life and lower operating costs by keeping the excavator on the jobsite moving material and generating rental fees, not in the shop for repairs.
By incorporating YNF Machinery’s high-quality products, such as excavator couplings and hydraulic cylinder seal kits, you can enhance your equipment’s performance and durability. These reliable solutions simplify maintenance and ensure your machine operates efficiently.
Adopting a proactive maintenance routine saves you money and prevents unexpected breakdowns. Simple steps like daily inspections, cleaning, and timely replacements keep your equipment in top condition. Start today to maximize efficiency and minimize costs.
FAQ
What is the best way to clean mini excavator undercarriage parts?
Use a high-pressure washer to remove mud and debris. For tight spaces, use stiff brushes or undercarriage cleaners. After cleaning, inspect for hidden damage and dry the parts thoroughly to prevent rust. Regular cleaning ensures optimal performance and longevity.
How often should you inspect undercarriage parts?
Perform daily visual checks before each shift. Conduct detailed inspections weekly or monthly, depending on usage. For heavily used machines, inspect every 1,000 to 2,000 hours. Regular inspections help you catch issues early and avoid costly repairs.
How do you know when to replace undercarriage parts?
Replace parts when they reach 100% wear. Look for signs like cracks, uneven wear, or missing teeth. Delaying replacement risks further damage and increases downtime. Regular monitoring helps you plan replacements efficiently.
Why is track tension important for mini excavators?
Proper track tension prevents unnecessary wear and ensures smooth operation. Loose tracks can slip off rollers, while tight tracks strain components. Regularly measure track sag and adjust tension to match the manufacturer’s recommendations.
Why choose YNF Machinery for replacement parts?
YNF Machinery offers high-quality parts that meet or exceed industry standards. Their products, like hydraulic cylinder seal kits and excavator couplings, ensure durability and reliability. Competitive pricing and excellent customer support make them a trusted choice for contractors worldwide.